Successful 70 surfaces production before Chinese New Year
Dear LaMetric Backers,
We hope you are doing well and enjoyed the Christmas and New Year holidays!
Every day we are getting closer to the final result and mass production for our backers. As it was mentioned in the previous update, the iOS app is officially finished and working smoothly; we have tested each light effect, significantly improved the Flags of the World, and created a beautiful Patchwork Quilt effect, which will add much more versatility to your space! On top of that, we have reached the best look of the product, checked how the parts work together, and now moving forward to the manufacturing phase.
Today, we are carrying out the last steps before mass production for our backers, so we would like to share our progress with you!
Our main priority is to provide our customers with the highest possible quality product. As we faced remote manufacturing due to COVID-19, we decided to start with a trial production in limited quantity to verify manufacturing processes and product quality before launching full-scale mass production for our bakers. We bought the needed quantity of long-awaiting components due to chip shortage from the spot market and produced 70 surfaces to execute reliability tests by our supplier, perform certification by an accredited laboratory, verify manufacturing processes and check the final quality in our headquarters. These steps should make us confident in controlling the product quality and producing the full-scale batch for backers.
Great result starts from the excellent processes
Before launching the manufacturing trial, our team had developed the set of Manufacturing Diagrams, which covers all manufacturing and test phases and guides the supplier along the way. It allows the manufacturer partner to meet our quality expectations at every stage of the process.

One of the SKY Manufacturing Process (information is blurred due to confidentiality)
We designed our processes with the involvement of information technologies which help factory staff to avoid human errors and quickly detect manufacturing process deviations: every single product’s component has a barcode, every single manufacturing step is logged to the Cloud IT System that strictly controls the order of operations and verifies test results.
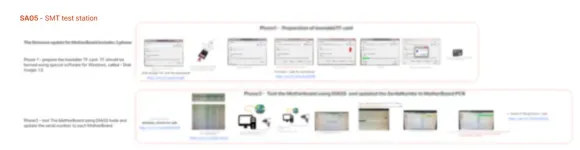
One of the SKY Test Process (information is bloored due to confidentiality)
The heart of the SKY
The manufacturing trial started at the beginning of the year from the printed circuit board production, which lays the basis for the device. Our manufacturer partner made the unique photos straight from the factory floor to demonstrate to you the process of SKY “heart” production. Let’s take a look at the manufacturing journey of assembling SKY printed circuit boards:
1. First of all, the printed circuit boards get produced

2. The solder paste is applied on the printed circuit boards

3. Then, the pick & place machine puts all the components in suitable locations on the printed circuit boards
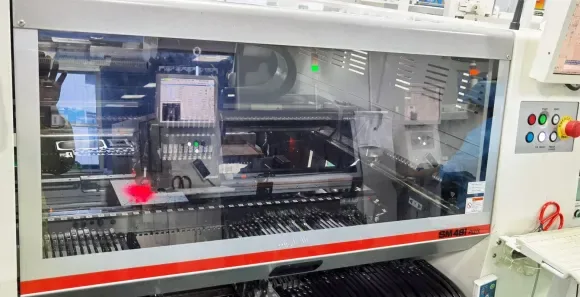
4. Finally, the printed circuit board with components goes into the oven for soldering, and we have electronics ready that put life into the SKY.

Proprietary defects detection technology
After production, printed circuit boards might have defects. To test every single board our team developed the proprietary set of hardware fixtures and the diagnostic software. It helps verify whether each function works correctly and catch defective ones before assembling inside the enclosure. Such testing significantly minimizes the probability of product defects and makes sure all technical abilities are in running order. If the board passes the test, then its life path continues.
Check out how testing is performed on the fresh-baked SKY printed circuit boards:

Moreover, our diagnostic software sends the reports to the Сloud IT System, which allows reviewing testing results from the headquarters, being thousands of miles away.

Mechanical parts with the final look & feel
In the previous update we showed photos of the pilot plastic batch and molds - big pieces of steel, used to produce them. This time we produced 70 sets of mechanical parts with the final finish and improvements made after given feedback.

These parts were used to assemble 70 pilot surfaces.
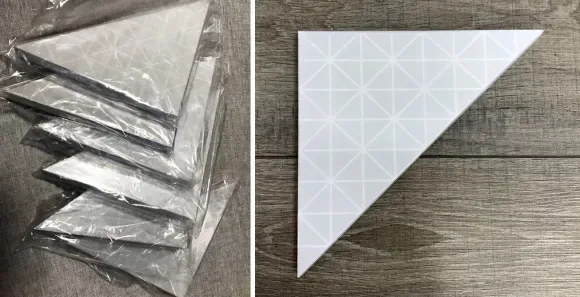
Reliability tests for SKY surfaces
Our manufacturer partner assembled 70 surfaces and already started to conduct reliability tests.
In the video, you can observe the drop test where the SKY surface falls from different heights to which it can be subjected during real use. This test finds out whether the surface remains assembled after the series of drop tests.
It’s also important to conduct the aging test where the surfaces light up for more than 24 hours.
Sustainable and reliable packaging
It is also vital to create safe and reliable packaging ready for any type of logistics. For this reason, our engineers developed the packaging, which will protect the product against shaking during various transportations.
Besides 70 surfaces, we also produced packaging samples and are awaiting them in headquarters to make the final check of its reliability and adjust dimensions if needed.
As a sustainable Brand that produces versatile products to replace single-feature products, we are also using recyclable materials in package production.
Google Assistant and Amazon Alexa Smart Home skills
In parallel with the manufacturing trial, we have been working on Google Assistant and Amazon Alexa Smart Home Skills and would like to announce they have been released and certified by Google and Amazon this week!

Final steps before the mass production for backers
Our whole team was working very hard to speed up the manufacturing trial before the Chinese Happy New Year. We successfully reached the goal, manufactured 70 surfaces for the following tasks:
- The first set of surfaces is ready to start the certification process in the laboratory next week
- The second set of surfaces is being reliability tested out by our Manufacturing Partner
- The third set of surfaces is heading to our headquarters for final check and review to adjust manufacturing processes if needed
The plan is to wait for feedback from the laboratory to make sure surfaces pass the regulatory tests. Immediately after passing the tests, we would like to start mass production for backers. Luckily the final quantity of long-awaited components should come next month!
We stay open and transparent with our backers on every single step in the progress and would like to thank you a lot for your patience and tolerance! It is really important for us to manufacture the quality product to see You satisfied. We are kindly asking for the understanding for a little more time, while we are doing our finishing touches before the mass manufacturing for backers.
The truly long path of planning, creation and manufacturing has almost passed. We want our owners to obtain the best authentic lighting and home decoration as well, which will fascinate your home with its winning design. We are working hard to get a fantastic result and to deliver soon to your home a significant piece of our company's soul!
Products